Introduction
Smoothed Particle Hydrodynamics (SPH) has established itself as a crucial method for tackling some of the most demanding challenges in computational fluid dynamics (CFD). Unlike traditional mesh-based approaches, SPH models fluids as discrete particles, particularly suited for complex systems with intricate geometries and dynamic interactions. Industries across the globe are now adopting SPH to achieve faster, more accurate simulations.
This blog explores how SPH is being applied in real-world scenarios, with insights from our recent podcast featuring Andreas Bauer, Design Engineer at Kessler & Co, a leading manufacturer of drivetrain and powertrain components for heavy mobility vehicles. Andreas reveals how cloud-native SPH simulation software is accelerating their transmission design process. By achieving highly accurate simulations faster than ever with Dive CAEβs advanced simulation software, Kessler & Co is redefining innovation in drivetrain technology.
So, letβs dive into it!
What is SPH?
Smoothed Particle Hydrodynamics (SPH) is a computational method that simulates fluids and other continua by representing them as particles that interact through smoothing kernels. It is a mesh-free approach that handles complex boundaries, large deformations, and free-surface flows.
SPH offers a way to overcome the limitations of mesh-based methods, which can struggle with large systems or complex scenarios like oil flow in gearboxes or thermal management in wet disk brakes. By representing fluids as particles, SPH removes the constraints of predefined grids, allowing for a more natural representation of fluid behaviors. This flexibility has made it a preferred choice for engineers looking to simulate real-world conditions more effectively.
For more on the basics of SPH, watch this 1-minute explanatory video by Dive.
Faster Simulations with Cloud-Based and GPU-Powered Tools
Modern SPH tools, such as DiveCAE, have further enhanced the applicability of this method by integrating cloud computing and GPU acceleration. These advancements have drastically reduced simulation times, enabling engineers to complete tasks in hours that previously took days. As Andreas Bauer from Kessler & Co highlighted, DiveCAEβs cloud-native infrastructure has eliminated their need for heavy hardware investments, making high-fidelity simulations accessible without costly local resources. Additionally, the GPU server is giving β5 to 10 times speed-ups,β transforming their daily workflows and enabling engineers to iterate designs far more efficiently.
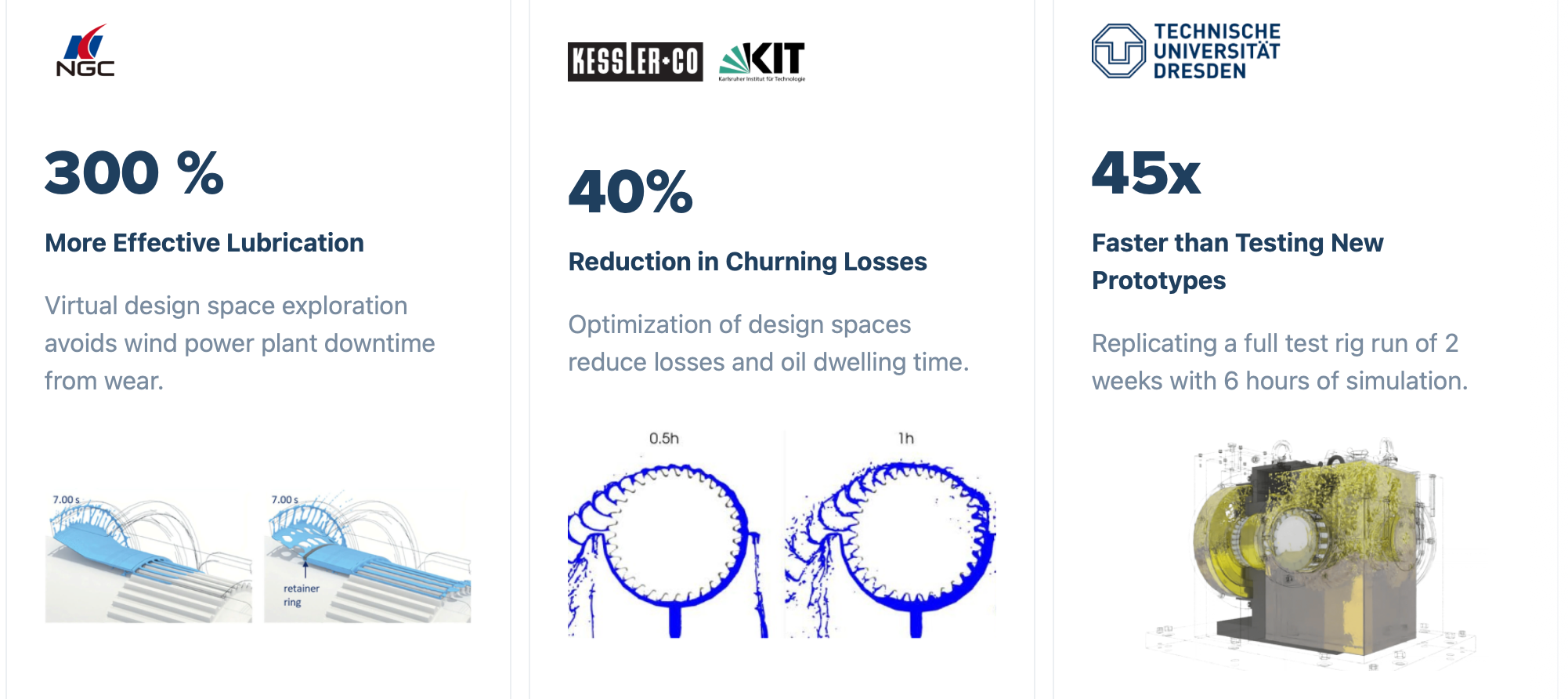
The ability to run multiple simulations in parallel is another game-changing feature of these tools. Engineers can now test different operational points or design configurations simultaneously, ensuring that their products are optimized for a wide range of scenarios. This parallelization saves time and enhances confidence in the final design.
Practical Applications in Engineering
One of the most impactful uses of SPH is in gearbox design. Engineers rely on SPH to visualize oil flow within gearboxes, identifying areas with insufficient lubrication or excessive energy loss. This detailed insight allows for targeted improvements, such as optimizing the placement of components to ensure proper lubrication and minimize heat buildup.
Advanced simulation capabilities of DiveCAE on the dynamics of a formula gearbox
Another critical application is in the thermal management of wet disk brakes. With SPH, engineers can analyze how design variations affect cooling efficiency. This capability ensures that products meet safety standards while also extending their operational lifespan. These insights, which were previously inaccessible or required extensive physical testing, are now readily available through simulation.
The iterative nature of SPH-based workflows allows engineers to modify designs based on simulation results and quickly re-run the tests. This approach not only accelerates product development but also ensures higher-quality outcomes. Engineers can evaluate their designs across a broader spectrum of conditions, leading to more robust and reliable products.
Reducing Costs and Enhancing Decision-Making
SPH tools also simplify communication between teams. The intuitive visualization of simulation results makes it easier for engineers to share findings with non-experts, fostering collaboration across departments. Whether itβs a design tweak in a CAD model or a change in operational parameters, the seamless integration of SPH results into the workflow streamlines decision-making.
The cost-effectiveness of SPH cannot be overlooked. By reducing the need for expensive physical testing and minimizing hardware requirements, tools like Dive allow organizations to allocate resources more efficiently. Engineers can focus on refining their designs while relying on accurate, virtual simulations to validate their choices.
A demo video highlighting the ability of DiveCAE to simulate complex movements and velocity fields with accuracy and detail.
Conclusion
Smoothed Particle Hydrodynamics (SPH) has proven to be a significant advancement in computational fluid dynamics, providing exceptional flexibility, accuracy, and efficiency for tackling complex engineering challenges. With tools like DiveCAE, engineers can achieve faster simulations, eliminate costly hardware investments, and collaborate seamlessly across teams. Insights from Andreas Bauer at Kessler & Co demonstrate how SPH is changing workflows, enabling more robust designs and reducing development timelines. As industries continue to adopt SPH, its impact on engineering efficiency and product quality will only grow, making it an essential tool for modern design and simulation.
For more insights, watch the podcast featuring Andreas Bauer
..or explore DiveCAE to see how it can transform your simulation workflows: https://www.divecae.com